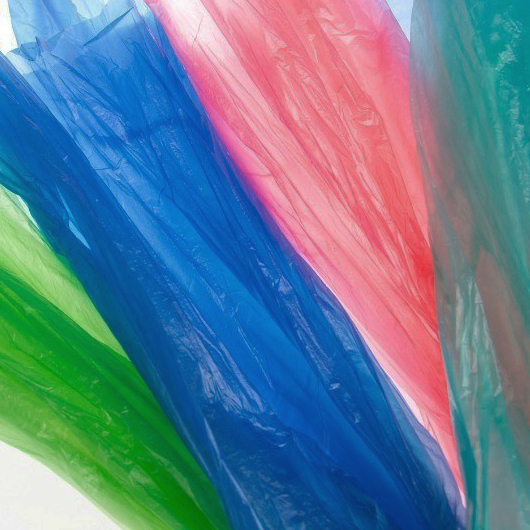
Polypropylene
Polypropylene (or polypropene), abbreviated as PP, is a widely used semi-crystalline thermoplastic polymer that appeared in the 50s. To make polypropylene, propylene must be cured with a catalyst or metallocene. It accounts for around 19% of demand in Europe, making it the number 2 most widely used plastic on the continent.
PP is highly versatile and therefore ideal for many uses in various sectors: the automotive industry, cosmetics, pharmaceuticals, agri-food, electronics, furniture and decorative textiles.
Pros
Polypropylene is translucent to opaque, hydrophobic, solid, semi-rigid and highly abrasion resistant. It cannot be torn, remains firm in the face of wear and bending, and is very easily coloured for customisation options.
Its resistance to salts, acids and alkalis means it can be used in a range of ways. Physiologically flawless, odourless, sterilisable and non-toxic, PP is ideal for products that come into contact with food or cosmetics. It is extremely heat resistant (not melting until 160°C).
Some plastics made from polyethylene (PE) and polypropylene (PP) have been chosen to be collected separately and reused. Once isolated, the PP is ground, washed and dried. The polypropylene plastic pellets obtained are used to supply various industries with recycled raw materials.
It is also a cheap material.
Cons
Mass production of polypropylene has a big impact on the environment and consumes a lot of petroleum, as well as causing greenhouse gas emissions. This polymer is theoretically non-toxic in its pure state, but can become toxic depending on the additives used to change its properties.
PP is fragile (brittle) at low temperatures, because its transition point is close to room temperature. It is sensitive to UV and weather and less resistant to oxidation than PE.
We can make your next PP items, but we can also offer you in particular new recycled or non-fossil-derived materials to help you reduce your environmental footprint. Feel free to contact us to discuss your future project.